Introduction
Spray cans are ubiquitous in our daily lives, found in everything from deodorants and air fresheners to paints and insecticides. The magic behind these cans lies in the propellants and gases that power them. These substances are responsible for expelling the product from the can in a fine mist or spray, making them incredibly convenient and efficient. Understanding the intricacies of spray can propellants and gases is essential for appreciating their role in various applications and their impact on the environment.
The journey of spray can technology began in the early 20th century, with significant advancements over the decades. Initially, these cans were simple devices, but technological innovations have transformed them into sophisticated tools. The propellants used in spray cans are responsible for expelling the product from the can, ensuring a consistent and controlled spray.
Spray can propellants can be broadly categorized into two types: compressed gases and liquefied gases. Each type has its unique properties and applications. Compressed gases, such as nitrogen and carbon dioxide, are commonly used for their stability and safety. On the other hand, liquefied gases, including hydrocarbons and hydrofluorocarbons (HFCs), offer higher pressure and better performance.
The environmental impact of spray can propellants has been a topic of concern for many years. The use of chlorofluorocarbons (CFCs) in the past led to significant ozone depletion, prompting the development of more eco-friendly alternatives. Today, the focus is on reducing the global warming potential (GWP) of propellants and finding sustainable solutions.
Safety considerations are paramount when dealing with spray can propellants. Proper handling, storage, and awareness of health risks are essential to prevent accidents and ensure user safety. Regulations and standards at both international and national levels govern the use of these propellants, ensuring compliance with safety and environmental guidelines.
Innovations in propellant technology continue to drive the industry forward. Eco-friendly alternatives, such as compressed air and water-based propellants, are gaining popularity. Advances in safety features, such as pressure relief valves and tamper-proof designs, enhance the overall reliability of spray cans.
Spray cans find applications in various sectors, including household products like air fresheners and cleaning agents, as well as industrial uses such as paints and lubricants. The advantages of using spray cans include their convenience, efficiency, and ability to deliver a consistent product application.
However, challenges and limitations persist. Environmental concerns, safety issues, and the need for sustainable propellants are ongoing challenges that the industry must address. Future trends point towards the development of more sustainable propellants and technological advancements that enhance the performance and safety of spray cans.
In this comprehensive guide, we will delve into the history, types, mechanisms, environmental impact, safety considerations, regulations, innovations, applications, advantages, challenges, and future trends of spray can propellants and gases. We will also explore case studies and answer common questions to provide a thorough understanding of this essential topic.
History of Spray Can Propellants
The history of spray can propellants dates back to the early 20th century when the first aerosol spray can was invented. In 1927, Norwegian engineer Erik Rotheim patented the first aerosol can and valve design, which laid the foundation for modern spray cans. This invention allowed for the controlled release of liquids and gases, revolutionizing various industries.
During World War II, the need for portable insecticides for soldiers led to the development of the “bug bomb,” a precursor to modern aerosol cans. The bug bomb used a combination of liquefied gas and insecticide, providing an effective solution for pest control in military settings.
The post-war era saw significant advancements in spray can technology. In the 1950s, the introduction of chlorofluorocarbons (CFCs) as propellants marked a turning point. CFCs offered excellent performance and stability, making them the preferred choice for many applications. However, the environmental impact of CFCs, particularly their role in ozone depletion, became a major concern in the 1970s.
The discovery of the ozone hole over Antarctica in the 1980s led to international efforts to phase out CFCs. The Montreal Protocol, signed in 1987, was a landmark agreement that aimed to reduce and eventually eliminate the use of ozone-depleting substances. This prompted the development of alternative propellants, such as hydrofluorocarbons (HFCs) and hydrocarbons, which have a lower impact on the ozone layer.
Types of Propellants
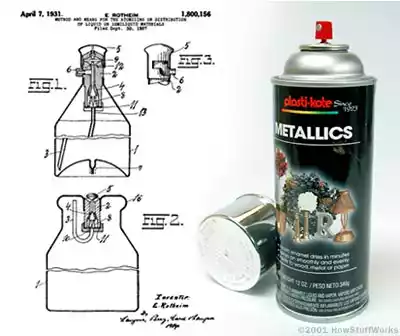
Spray can propellants can be classified into two main types: compressed gases and liquefied gases. Each type has distinct characteristics and applications.
Compressed Gases
Compressed gases are stored in their gaseous state under high pressure. Common examples include nitrogen, carbon dioxide, and nitrous oxide. These gases are known for their stability and safety, making them suitable for various applications.
• Nitrogen: Nitrogen is an inert gas that does not react with the product inside the can. It is commonly used in food packaging and medical applications due to its non-reactive nature.
• Carbon Dioxide: Carbon dioxide is used in products like whipped cream and carbonated beverages. It provides the necessary pressure to expel the product while maintaining its quality.
• Nitrous Oxide: Nitrous oxide is used in culinary applications, such as whipped cream dispensers. It is also used in some medical applications as an anesthetic.
Liquefied Gases
Liquefied gases are stored in their liquid state under pressure. When released, they vaporize and create the necessary pressure to expel the product. Common examples include hydrocarbons, hydrofluorocarbons (HFCs), and dimethyl ether (DME).
• Hydrocarbons: Hydrocarbons, such as propane, butane, and isobutane, are widely used due to their low cost and high efficiency. They are commonly found in household products like air fresheners and hair sprays.
• Hydrofluorocarbons (HFCs): HFCs, such as HFC-134a, are used as alternatives to CFCs. They have a lower impact on the ozone layer but still contribute to global warming. HFCs are used in applications like refrigeration and air conditioning.
• Dimethyl Ether (DME): DME is a versatile propellant used in various applications, including personal care products and industrial sprays. It is known for its low toxicity and environmental impact.
Common Propellants Used in Spray Cans
Several propellants are commonly used in spray cans, each with its unique properties and applications.
Hydrocarbons
Hydrocarbons, such as propane, butane, and isobutane, are among the most widely used propellants. They offer several advantages, including low cost, high efficiency, and compatibility with a wide range of products. Hydrocarbons are commonly used in household products like air fresheners, hair sprays, and insecticides.
• Propane: Propane is a highly efficient propellant that provides excellent pressure and performance. It is commonly used in products like cooking sprays and air fresheners.
• Butane: Butane is another popular hydrocarbon propellant known for its high pressure and stability. It is used in products like hair sprays and deodorants.
• Isobutane: Isobutane is a branched-chain hydrocarbon that offers similar properties to butane. It is used in various applications, including personal care products and household sprays.
Hydrofluorocarbons (HFCs)
Hydrofluorocarbons (HFCs) are used as alternatives to chlorofluorocarbons (CFCs) due to their lower impact on the ozone layer. However, HFCs still contribute to global warming, and efforts are ongoing to find more sustainable alternatives. Common HFCs used in spray cans include HFC-134a and HFC-152a.
• HFC-134a: HFC-134a is a widely used propellant in applications like refrigeration, air conditioning, and aerosol sprays. It offers excellent performance and stability but has a high global warming potential.
• HFC-152a: HFC-152a is a lower GWP alternative to HFC-134a. It is used in various applications, including personal care products and household sprays.
Dimethyl Ether (DME)
Dimethyl Ether (DME) is a versatile propellant known for its low toxicity and environmental impact. It is used in various applications, including personal care products, industrial sprays, and household products. DME offers excellent solubility and compatibility with a wide range of formulations.
Mechanism of Action
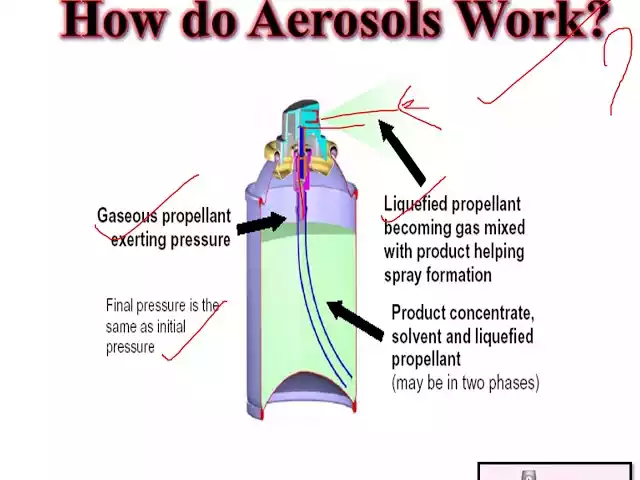
The mechanism of action of spray can propellants involves the creation of pressure to expel the product from the can. This process is influenced by the type of propellant used and the design of the spray can.
How Propellants Work
When the valve of a spray can is pressed, the propellant inside the can creates pressure that forces the product out through the nozzle. The propellant can be in the form of a compressed gas or a liquefied gas. In the case of compressed gases, the pressure is generated by the gas itself. For liquefied gases, the pressure is created by the vaporization of the liquid propellant.
The Role of Pressure
Pressure is a critical factor in the functioning of spray cans. The pressure inside the can must be sufficient to expel the product in a controlled and consistent manner. The design of the valve and nozzle also plays a crucial role in determining the spray pattern and droplet size.
Environmental Impact
The environmental impact of spray can propellants has been a topic of concern for many years. The use of chlorofluorocarbons (CFCs) in the past led to significant ozone depletion, prompting the development of more eco-friendly alternatives.
Ozone Depletion
Chlorofluorocarbons (CFCs) were widely used as propellants in the mid-20th century due to their excellent performance and stability. However, the discovery of the ozone hole over Antarctica in the 1980s revealed the detrimental impact of CFCs on the ozone layer. The ozone layer protects the Earth from harmful ultraviolet (UV) radiation, and its depletion can lead to increased rates of skin cancer, cataracts, and other health issues.
Global Warming Potential
While hydrofluorocarbons (HFCs) were developed as alternatives to CFCs, they still contribute to global warming. HFCs have a high global warming potential (GWP), which means they trap heat in the atmosphere and contribute to climate change. Efforts are ongoing to find more sustainable alternatives with lower GWP.
Safety Considerations
Safety considerations are paramount when dealing with spray can propellants. Proper handling, storage, and awareness of health risks are essential to prevent accidents and ensure user safety.
Handling and Storage
Spray cans should be stored in a cool, dry place away from direct sunlight and heat sources. High temperatures can cause the pressure inside the can to increase, leading to the risk of explosion. It is also important to avoid puncturing or incinerating spray cans, as this can release the propellant and pose a safety hazard.
Health Risks
Some propellants, such as hydrocarbons and HFCs, can pose health risks if inhaled or ingested. Prolonged exposure to these substances can cause respiratory issues, dizziness, and other health problems. It is important to use spray cans in well-ventilated areas and follow the manufacturer’s instructions for safe use.
Regulations and Standards
Regulations and standards at both international and national levels govern the use of spray can propellants. These guidelines ensure compliance with safety and environmental requirements.
International Guidelines
The Montreal Protocol, signed in 1987, is a landmark international agreement that aims to reduce and eventually eliminate the use of ozone-depleting substances, including CFCs. The protocol has been successful in phasing out CFCs and promoting the use of more sustainable alternatives.
National Regulations
Many countries have implemented their own regulations and standards for the use of spray can propellants. These regulations may include restrictions on the use of certain substances, labeling requirements, and safety guidelines. It is important for manufacturers and users to comply with these regulations to ensure safety and environmental protection.
Innovations in Propellant Technology
Innovations in propellant technology continue to drive the industry forward. Eco-friendly alternatives, such as compressed air and water-based propellants, are gaining popularity. Advances in safety features, such as pressure relief valves and tamper-proof designs, enhance the overall reliability of spray cans.
Eco-friendly Alternatives
Eco-friendly alternatives to traditional propellants are being developed to reduce the environmental impact of spray cans. Compressed air and water-based propellants are among the most promising options. These alternatives offer similar performance to traditional propellants while minimizing their impact on the environment.
Advances in Safety
Advances in safety features, such as pressure relief valves and tamper-proof designs, enhance the overall reliability of spray cans. These features help prevent accidents and ensure the safe use of spray cans.
Applications of Spray Cans
Spray cans find applications in various sectors, including household products like air fresheners and cleaning agents, as well as industrial uses such as paints and lubricants.
Household Products
Spray cans are commonly used in household products like air fresheners, cleaning agents, and insecticides. These products offer convenience and efficiency, making them popular among consumers.
Industrial Uses
Spray cans are also used in industrial applications, such as paints, lubricants, and adhesives. These products provide a consistent and controlled application, making them ideal for various industrial processes.
Advantages of Using Spray Cans
The advantages of using spray cans include their convenience, efficiency, and ability to deliver a consistent product application.
Convenience
Spray cans offer convenience and ease of use, making them popular among consumers. They provide a quick and efficient way to apply products, reducing the time and effort required.
Efficiency
Spray cans provide a consistent and controlled application, ensuring that the product is evenly distributed. This makes them ideal for various applications, from household products to industrial uses.
Challenges and Limitations
Challenges and limitations persist in the use of spray can propellants. Environmental concerns, safety issues, and the need for sustainable propellants are ongoing challenges that the industry must address.
Environmental Concerns
The environmental impact of spray can propellants, particularly their contribution to ozone depletion and global warming, is a major concern. Efforts are ongoing to develop more sustainable alternatives that minimize their impact on the environment.
Safety Issues
Safety issues, such as the risk of explosion and health risks associated with inhalation or ingestion of propellants, are also important considerations. Proper handling, storage, and awareness of these risks are essential to ensure user safety.
Future Trends
Future trends point towards the development of more sustainable propellants and technological advancements that enhance the performance and safety of spray cans.
Sustainable Propellants
The development of sustainable propellants, such as compressed air and water-based alternatives, is a key focus for the industry. These alternatives offer similar performance to traditional propellants while minimizing their impact on the environment.
Technological Advancements
Technological advancements, such as improved valve and nozzle designs, are also driving the industry forward. These innovations enhance the performance and safety of spray cans, making them more reliable and efficient.
Case Studies
Case studies provide valuable insights into the successful implementation of spray can propellants and the lessons learned from these experiences.
Successful Implementations
Successful implementations of spray can propellants can be found in various industries, from household products to industrial applications. These case studies highlight the benefits and challenges of using spray cans and provide valuable lessons for future developments.
Lessons Learned
Lessons learned from these case studies can help guide the development of more sustainable and efficient spray can propellants. By understanding the successes and challenges of past implementations, the industry can continue to innovate and improve.
FAQs
What are the most common propellants used in spray cans?
The most common propellants used in spray cans include hydrocarbons (such as propane, butane, and isobutane), hydrofluorocarbons (HFCs), and dimethyl ether (DME). Hydrocarbons are widely used due to their low cost and high efficiency, while HFCs are used as alternatives to chlorofluorocarbons (CFCs) due to their lower impact on the ozone layer. DME is a versatile propellant known for its low toxicity and environmental impact.
How do spray can propellants work?
Spray can propellants work by creating pressure inside the can, which forces the product out through the nozzle when the valve is pressed. The propellant can be in the form of a compressed gas or a liquefied gas. In the case of compressed gases, the pressure is generated by the gas itself. For liquefied gases, the pressure is created by the vaporization of the liquid propellant.
What are the environmental impacts of spray can propellants?
The environmental impacts of spray can propellants include ozone depletion and global warming. Chlorofluorocarbons (CFCs), which were widely used in the past, contributed to significant ozone depletion. Hydrofluorocarbons (HFCs), which are used as alternatives to CFCs, have a high global warming potential and contribute to climate change. Efforts are ongoing to develop more sustainable alternatives with lower environmental impact.
What safety considerations should be taken when using spray cans?
Safety considerations when using spray cans include proper handling, storage, and awareness of health risks. Spray cans should be stored in a cool, dry place away from direct sunlight and heat sources. It is important to avoid puncturing or incinerating spray cans, as this can release the propellant and pose a safety hazard. Some propellants can pose health risks if inhaled or ingested.
What are the future trends in spray can propellant technology?
Future trends in spray can propellant technology include the development of more sustainable propellants, such as compressed air and water-based alternatives. Technological advancements, such as improved valve and nozzle designs, are also driving the industry forward. These innovations enhance the performance and safety of spray cans, making them more reliable and efficient.
Conclusion
Spray can propellants and gases play a vital role in the functionality and efficiency of spray cans. Understanding their history, types, mechanisms, environmental impact, safety considerations, regulations, innovations, applications, advantages, challenges, and future trends is essential for appreciating their significance. As the industry continues to evolve, the focus remains on developing more sustainable and efficient propellants that minimize environmental impact and enhance user safety.
Sources:
– EPA. “The Montreal Protocol on Substances that Deplete the Ozone Layer.” EPA
– National Institute for Occupational Safety and Health (NIOSH). “Aerosol Propellants.” NIOSH
– American Chemical Society. “The Chemistry of Aerosol Sprays.” [ACS](https://www.acs.org/content/acs/en/education/resources/highschool/chemmatters/past-issues/archive-2014-2015/aerosol-s
Propeller Overhaul – Grumman Style
Ruth Aquilani is a renowned graffiti artist known for her bold, colorful, and expressive style. She began her career as a street artist in the early 2000s, quickly making a name for herself in the graffiti community with her unique and striking works of art.
[…] for projects that require precision. However, with the use of stencils and masking techniques, spray paint can still be used for detailed […]