Introduction to Aerosol Spray Can Technology
Aerosol spray cans are ubiquitous in our daily lives, found in products ranging from deodorants to paint. The technology behind these cans is a fascinating blend of chemistry and engineering, designed to deliver a fine mist of liquid or powder. The concept of aerosol technology dates back to the early 20th century, with significant advancements during World War II when the need for portable insecticides became critical. The modern aerosol can, as we know it, was patented in 1941 by Lyle Goodhue and William Sullivan, revolutionizing the way products are dispensed.
The basic principle of an aerosol spray can involves a pressurized container that holds a product and a propellant. When the valve is activated, the propellant forces the product out of the can in a fine spray. This simple yet effective mechanism has made aerosol cans a staple in various industries, from personal care to automotive maintenance.
Understanding the science behind aerosol spray cans not only enhances our appreciation for this everyday item but also sheds light on the innovations and safety measures that ensure their efficient and safe use. Let’s delve deeper into the components, working mechanisms, and applications of aerosol spray cans.
Components of an Aerosol Spray Can
The Canister
The canister is the outer shell of the aerosol spray can, typically made from aluminum or steel. It is designed to withstand high pressure and prevent leaks. The choice of material depends on the product’s chemical properties and the required durability. Aluminum is lightweight and resistant to corrosion, making it ideal for personal care products. Steel, on the other hand, is more robust and often used for industrial applications.
The Propellant
The propellant is a crucial component that drives the product out of the can. It can be a compressed gas or a liquefied gas. Compressed gases like nitrogen and carbon dioxide are used for products that require a gentle spray. Liquefied gases, such as butane and propane, are more common and provide a consistent spray pattern. The choice of propellant affects the spray’s pressure, consistency, and environmental impact.
The Valve System
The valve system controls the release of the product. It consists of a valve cup, stem, and actuator. When the actuator is pressed, the valve opens, allowing the propellant to push the product out. The design of the valve system ensures a controlled and even spray. Different types of valves are used depending on the product’s viscosity and desired spray pattern.
The Product Formulation
The product formulation is the actual substance being dispensed. It can be a liquid, powder, or foam. The formulation is mixed with the propellant inside the can. The ratio of product to propellant is carefully calibrated to ensure optimal performance. Factors such as viscosity, solubility, and stability are considered during formulation to achieve the desired spray characteristics.
How Aerosol Spray Cans Work
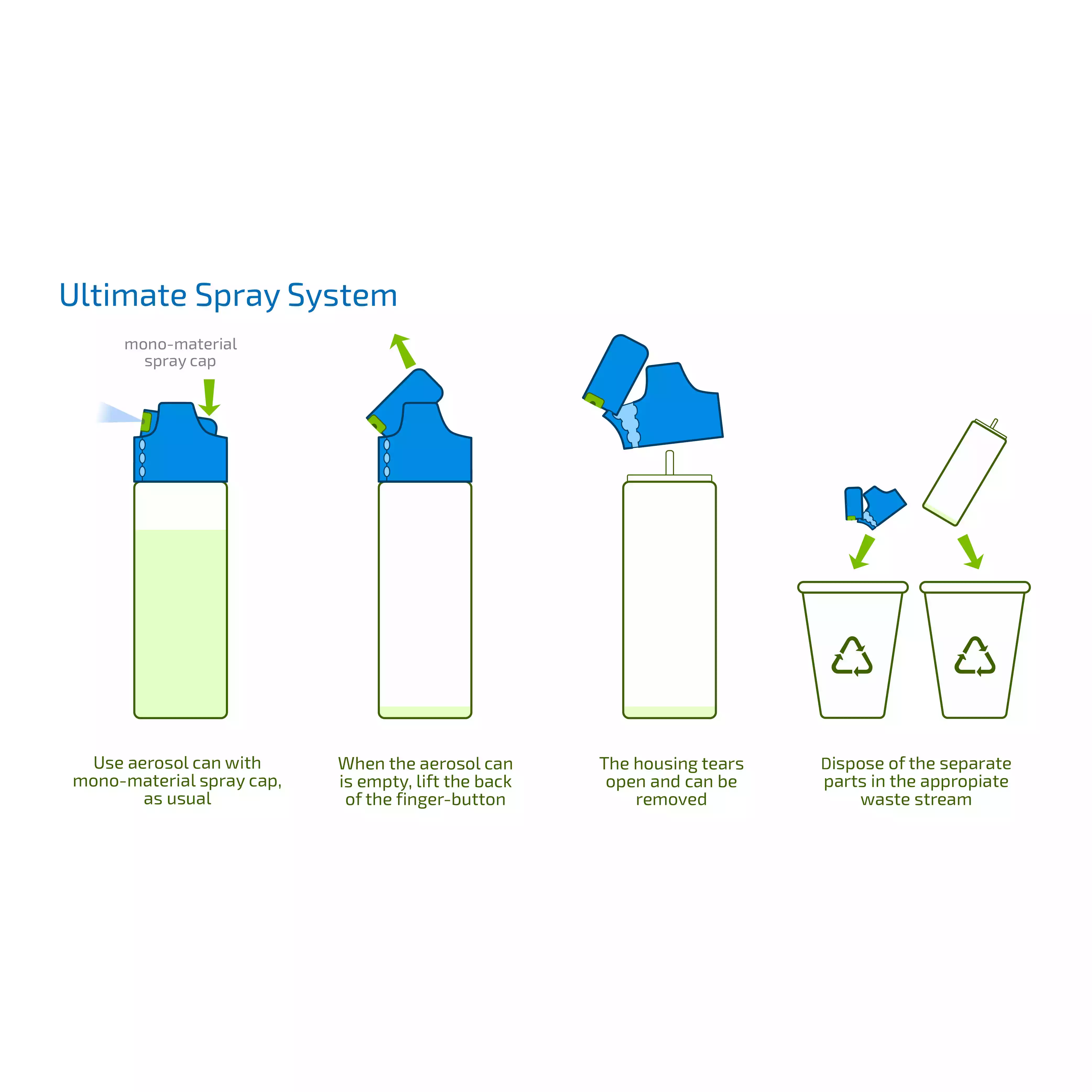
Pressurization Process
The pressurization process is fundamental to the operation of aerosol spray cans. The can is filled with the product and propellant under high pressure. The propellant exists in both liquid and gas phases within the can. When the valve is opened, the pressure difference forces the liquid product out, while the gas phase maintains the pressure inside the can. This continuous pressurization ensures a consistent spray until the can is empty.
Dispersion Mechanism
The dispersion mechanism involves the transformation of the liquid product into a fine mist. As the product exits the can, it passes through a nozzle that breaks it into tiny droplets. The design of the nozzle and the pressure of the propellant determine the size and distribution of the droplets. This mechanism is crucial for applications that require a uniform and controlled spray, such as paint or insecticides.
Types of Propellants Used in Aerosol Cans
Compressed Gases
Compressed gases like nitrogen, carbon dioxide, and nitrous oxide are used as propellants in aerosol cans. These gases are stored under high pressure and expand when released, pushing the product out of the can. Compressed gases are environmentally friendly and do not contribute to ozone depletion. However, they provide a lower pressure compared to liquefied gases, making them suitable for products that require a gentle spray.
Liquefied Gases
Liquefied gases such as butane, propane, and isobutane are more commonly used as propellants. These gases are stored in liquid form under pressure and vaporize when the valve is opened. Liquefied gases provide a higher pressure, resulting in a more forceful and consistent spray. However, they can contribute to environmental issues such as global warming and ozone depletion. Modern formulations often use hydrofluoroolefins (HFOs) as eco-friendly alternatives.
Applications of Aerosol Spray Cans
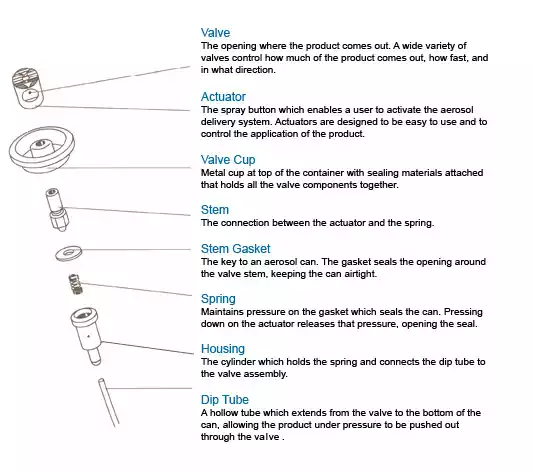
Household Products
Aerosol spray cans are widely used in household products such as air fresheners, cleaning agents, and insecticides. The convenience and effectiveness of aerosol sprays make them a popular choice for home use. Air fresheners, for example, deliver a fine mist that quickly disperses, neutralizing odors. Cleaning agents in aerosol form provide a targeted application, reducing waste and ensuring thorough coverage.
Industrial Uses
In industrial settings, aerosol spray cans are used for lubrication, painting, and surface treatments. Lubricants in aerosol form can reach tight spaces and provide a uniform coating, reducing friction and wear. Spray paints offer a smooth and even finish, making them ideal for touch-ups and small-scale projects. Surface treatments such as rust inhibitors and protective coatings are also commonly dispensed using aerosol cans.
Medical Applications
Aerosol technology plays a vital role in medical applications, particularly in the delivery of medications. Inhalers for asthma and chronic obstructive pulmonary disease (COPD) use aerosol spray cans to deliver precise doses of medication directly to the lungs. This method ensures rapid absorption and effective treatment. Other medical applications include topical anesthetics and wound care products.
Environmental Impact of Aerosol Spray Cans
Ozone Layer Depletion
Historically, aerosol spray cans used chlorofluorocarbons (CFCs) as propellants, which contributed to ozone layer depletion. The discovery of the ozone hole in the 1980s led to the phasing out of CFCs under the Montreal Protocol. Today, alternative propellants such as hydrofluorocarbons (HFCs) and hydrofluoroolefins (HFOs) are used. While HFCs do not deplete the ozone layer, they are potent greenhouse gases. HFOs, on the other hand, have a lower global warming potential and are considered more environmentally friendly.
Modern Eco-Friendly Alternatives
The aerosol industry has made significant strides in developing eco-friendly alternatives. Compressed gases like nitrogen and carbon dioxide are now used as propellants, reducing the environmental impact. Additionally, innovations in packaging and formulation have led to the creation of more sustainable aerosol products. For example, bag-on-valve (BOV) technology separates the product from the propellant, allowing for the use of compressed air as a propellant. This reduces the environmental footprint and improves product safety.
Safety Measures and Regulations
Handling and Storage
Proper handling and storage of aerosol spray cans are essential to ensure safety. Aerosol cans should be stored in a cool, dry place away from direct sunlight and heat sources. Overheating can cause the can to rupture, leading to potential injuries and property damage. It is also important to avoid puncturing or incinerating aerosol cans, as this can result in explosions. Always follow the manufacturer’s instructions for safe use and disposal.
Regulatory Standards
Aerosol spray cans are subject to strict regulatory standards to ensure safety and environmental compliance. In the United States, the Environmental Protection Agency (EPA) and the Consumer Product Safety Commission (CPSC) regulate aerosol products. These agencies set guidelines for propellant types, labeling, and disposal. Internationally, the European Union’s REACH regulation and the United Nations’ Globally Harmonized System (GHS) provide similar oversight. Compliance with these standards ensures that aerosol products are safe for consumers and the environment.
Innovations in Aerosol Technology
Smart Aerosol Systems
Advancements in technology have led to the development of smart aerosol systems. These systems incorporate sensors and microprocessors to deliver precise doses of product. For example, smart inhalers for asthma patients can track usage and provide real-time feedback, improving medication adherence. Other innovations include programmable aerosol dispensers for air fresheners and disinfectants, which can be controlled remotely via smartphone apps.
Sustainable Packaging Solutions
Sustainable packaging solutions are becoming increasingly important in the aerosol industry. Companies are exploring alternatives to traditional metal cans, such as biodegradable and recyclable materials. For instance, some aerosol products now use paper-based canisters or refillable containers. These innovations reduce waste and promote a circular economy. Additionally, advancements in valve and nozzle design have led to more efficient product delivery, minimizing the amount of propellant needed.
FAQs
What are the main components of an aerosol spray can?
An aerosol spray can consists of several key components: the canister, propellant, valve system, and product formulation. The canister is typically made of aluminum or steel and is designed to withstand high pressure. The propellant, which can be a compressed or liquefied gas, drives the product out of the can. The valve system controls the release of the product, ensuring a controlled and even spray. The product formulation is the actual substance being dispensed, such as a liquid, powder, or foam.
How do aerosol spray cans work?
Aerosol spray cans work through a pressurization process. The can is filled with the product and propellant under high pressure. When the valve is opened, the pressure difference forces the liquid product out, while the gas phase maintains the pressure inside the can. The product passes through a nozzle that breaks it into tiny droplets, creating a fine mist. This mechanism ensures a consistent and controlled spray until the can is empty.
What types of propellants are used in aerosol cans?
Aerosol cans use two main types of propellants: compressed gases and liquefied gases. Compressed gases like nitrogen and carbon dioxide are stored under high pressure and expand when released, pushing the product out of the can. Liquefied gases such as butane and propane are stored in liquid form under pressure and vaporize when the valve is opened. Compressed gases are environmentally friendly and provide a gentle spray, while liquefied gases offer a more forceful and consistent spray.
What are the environmental impacts of aerosol spray cans?
The environmental impact of aerosol spray cans depends on the type of propellant used. Historically, aerosol cans used chlorofluorocarbons (CFCs), which contributed to ozone layer depletion. Today, alternative propellants such as hydrofluorocarbons (HFCs) and hydrofluoroolefins (HFOs) are used. While HFCs do not deplete the ozone layer, they are potent greenhouse gases. HFOs have a lower global warming potential and are considered more environmentally friendly. The industry is also exploring eco-friendly alternatives like compressed gases and sustainable packaging solutions.
What safety measures should be taken when using aerosol spray cans?
Proper handling and storage of aerosol spray cans are essential to ensure safety. Store aerosol cans in a cool, dry place away from direct sunlight and heat sources. Avoid puncturing or incinerating aerosol cans, as this can result in explosions. Always follow the manufacturer’s instructions for safe use and disposal. Regulatory standards set by agencies like the Environmental Protection Agency (EPA) and the Consumer Product Safety Commission (CPSC) ensure that aerosol products are safe for consumers and the environment.
Conclusion
Aerosol spray can technology is a remarkable blend of chemistry and engineering, providing a convenient and effective way to dispense a wide range of products. From household items to medical applications, aerosol cans have become an integral part of our daily lives. Understanding the components, working mechanisms, and environmental impact of aerosol spray cans enhances our appreciation for this everyday item. Innovations in smart aerosol systems and sustainable packaging solutions continue to drive the industry forward, ensuring that aerosol products remain safe, efficient, and environmentally friendly.
Sources:
– Healthline. “The Benefits of Eating Vegetables.” Healthline.
– Environmental Protection Agency. “Aerosol Cans.” EPA.
– Consumer Product Safety Commission. “Aerosol Products.” CPSC.
– European Chemicals Agency. “REACH Regulation.” ECHA.
– United Nations. “Globally Harmonized System of Classification and Labelling of Chemicals (GHS).” UN.
Day 1 Tutorials on Aerosol Science and Technology
Ruth Aquilani is a renowned graffiti artist known for her bold, colorful, and expressive style. She began her career as a street artist in the early 2000s, quickly making a name for herself in the graffiti community with her unique and striking works of art.